Comprehending Porosity in Welding: Checking Out Causes, Results, and Avoidance Strategies
As experts in the welding market are well aware, comprehending the reasons, results, and avoidance techniques associated to porosity is important for attaining durable and reputable welds. By diving right into the origin causes of porosity, examining its damaging impacts on weld top quality, and discovering efficient avoidance approaches, welders can boost their knowledge and skills to create high-quality welds regularly.
Typical Root Causes Of Porosity
Contamination, in the form of dust, grease, or corrosion on the welding surface area, creates gas pockets when warmed, leading to porosity in the weld. Incorrect shielding happens when the securing gas, typically made use of in processes like MIG and TIG welding, is unable to completely protect the molten weld swimming pool from responding with the surrounding air, resulting in gas entrapment and succeeding porosity. Furthermore, poor gas coverage, typically due to wrong flow prices or nozzle positioning, can leave parts of the weld unguarded, permitting porosity to form.
Impacts on Weld High Quality
The existence of porosity in a weld can substantially endanger the total quality and stability of the welded joint. Porosity within a weld develops gaps or cavities that compromise the structure, making it more prone to cracking, rust, and mechanical failure. These spaces function as stress and anxiety concentrators, reducing the load-bearing capability of the weld and boosting the probability of early failing under used tension. Additionally, porosity can likewise offer as possible websites for hydrogen entrapment, additional worsening the destruction of the weld's mechanical properties.
Furthermore, porosity can hinder the efficiency of non-destructive screening (NDT) strategies, making it challenging to find other issues or suspensions within the weld. This can lead to substantial safety and security worries, particularly in vital applications where the structural honesty of the bonded components is critical.
Avoidance Techniques Introduction
Provided the damaging effect of porosity on weld high quality, effective avoidance methods are essential to maintaining the architectural stability of welded joints. Among the main prevention strategies is detailed cleansing of the base materials before welding. Impurities such as oil, grease, corrosion, and wetness can contribute to porosity, so making certain a tidy work surface area is important. Correct storage space of welding consumables in completely dry conditions is likewise essential to stop wetness absorption, which can result in gas entrapment throughout welding. In addition, selecting the proper welding parameters, such as voltage, existing, and take a trip speed, can aid reduce the threat of porosity formation. Making certain appropriate shielding gas circulation and coverage is one more essential prevention strategy, as not enough gas protection can lead to climatic contamination and porosity. Finally, appropriate welder training and accreditation are important for implementing safety nets effectively and constantly. By including these avoidance techniques into welding methods, the incident of porosity can be significantly minimized, causing more powerful and more trustworthy bonded joints.
Value of Appropriate Protecting
Proper shielding in welding plays an important function in stopping atmospheric contamination and ensuring the integrity of bonded joints. Securing gases, such as argon, helium, or a blend of both, are typically used to protect the weld pool from reacting with elements airborne like oxygen and nitrogen. When these reactive components enter contact with the hot weld swimming pool, they can trigger porosity, resulting in weak welds with decreased mechanical residential properties.
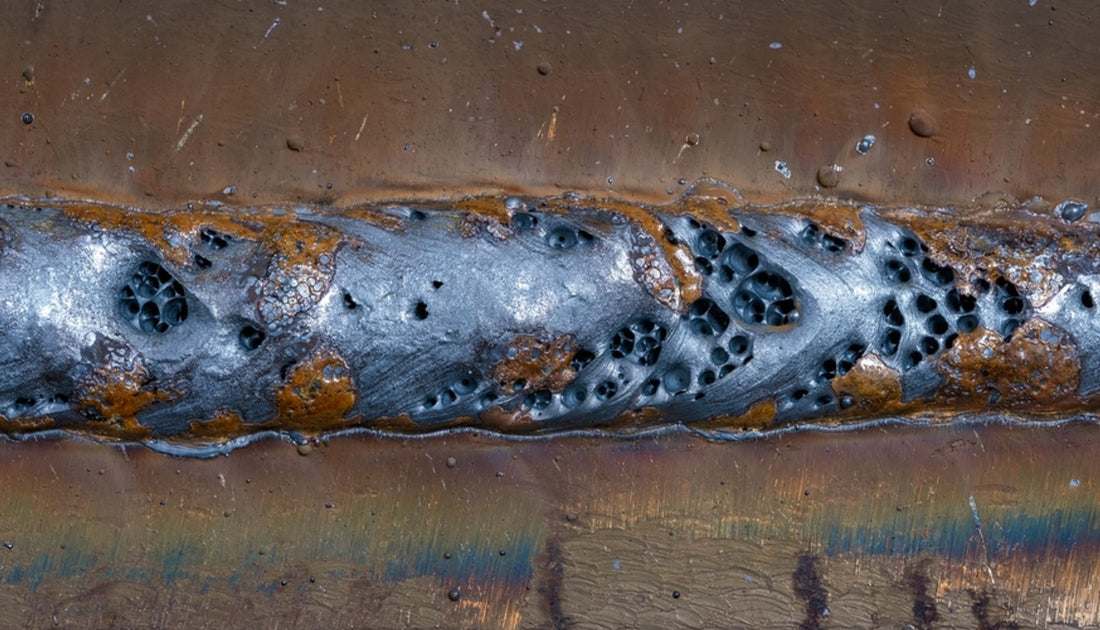
Poor securing can lead to different defects like porosity, spatter, and oxidation, endangering the structural stability of the bonded joint. As a result, adhering to appropriate securing methods is necessary to create top quality welds with marginal problems and make certain the longevity and dependability of the bonded components (What is Porosity).
Surveillance and Control Methods
Just how can welders effectively monitor and manage the welding procedure to make sure ideal results and avoid issues like porosity? By continually checking these variables, welders can recognize variances from the suitable problems and make instant modifications to stop porosity formation.

Additionally, implementing correct training programs for welders is crucial for monitoring and controlling the welding procedure successfully. What is Porosity. Educating welders on the importance of keeping regular criteria, such as appropriate gas shielding and take a trip rate, can help prevent porosity concerns. Routine analyses and qualifications can also make certain that welders are skillful in tracking and controlling welding procedures
Additionally, making use of automated welding systems can more information improve monitoring and control capabilities. These systems can specifically regulate welding criteria, decreasing the likelihood of human mistake and ensuring regular weld high quality. By incorporating sophisticated surveillance innovations, training programs, and automated systems, welders can properly keep track of and control the welding procedure to minimize porosity flaws and attain top notch welds.
Conclusion
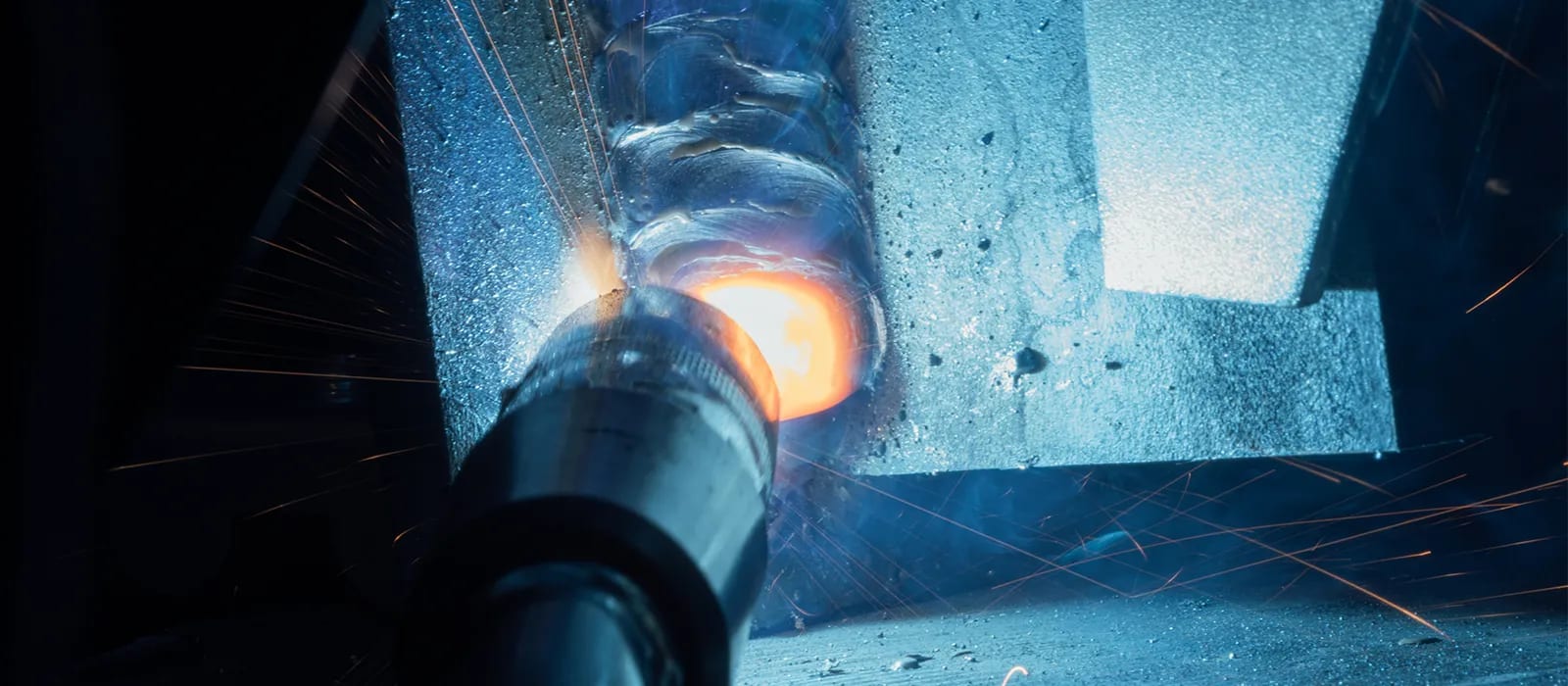
Comments on “Just how to Recognize What is Porosity in Welding and Improve Your Strategy”